1 半闭环控制系统原理
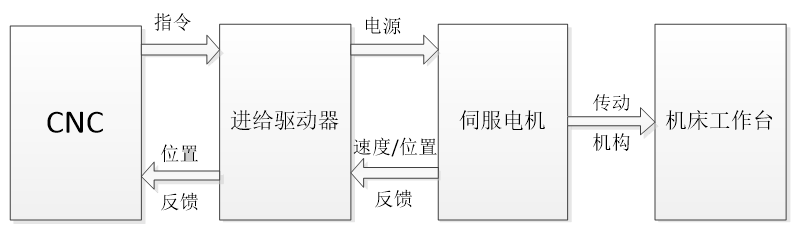
使用脉冲接口式伺服驱动器时有关参数需在驱动器上调节(例如:位置环开环增益,位置环前馈增益,速度环比例增益等)。
2 位置模式下驱动器的必要接线
在半闭环控制系统中,位置模式下驱动器X4口(MINAS-A5)根据其控制原理至少需要接入如下三种信号:
(1) 上位机的脉冲信号;
(2) 伺服使能(SRV-ON)信号;
(3) 输入信号共阳端。
由于SRV-ON信号接通后,电机绕组通电允许接受上位机控制指令,根据指令,电机进行相应的转动;否则电机绕组断电,电机处于自由状态(脱机状态),位置偏差清零,不接受指令。
对于其他驱动器的开关量控制信号如报警清除、驱动禁止、伺服准备等信号则根据实际需要接入。
例如对于报警清除输入信号,其是当驱动器出现报警时,确定报警已经排除后,上位机可利用该信号在不断电的情况下,清除某些故障报警,从而使位置误差清零,驱动器复位返回运行状态。
3 伺服系统上电时序
下图为驱动器的上电时序。控制电路的电源L1C/L2C同时或先于主电路电源L1/L2/L3接通。如果仅接通控制电路的电源,伺服准备(SRV-RDY)信号无效。
主电源接通后延迟一段时间(>10ms),伺服准备好信号有效,此时可以接受伺服使能(SRV-ON)信号,驱动器接收使能信号,电机绕组通电,允许接受上位机指令;否则电机处于自由状态。
当系统上电后,对于驱动器来说,完成上电初始化后,可以正常运行时,其输出信号中的SRV-RDY会给上位机一个低电平(0V),这样数控系统会由其输入输出口Y0.2(伺服运行允许)给驱动器的使能信号引脚29脚(森床驱动器为9脚)一个低电平,让其对应的光电耦合器导通,从而驱动器会控制电机绕组通电。其具体的上电时序如下图
4 回路原理
信号的连接,主要遵循回路原理。下表3.5所示为输入输出信号回路,针对驱动器的输入输出控制接口,其输入输出的信号电压是12-24V,接线时需要知道该引脚的功能以及电平匹配。
(1) 输入信号连接回路
电流从7脚(COM+)输入,如果29脚(SRV-ON)信号接地则左侧构成回路,进而光耦导通,内部接收到使能信号并进行相应动作。以SRV-ON信号为例
(2) 输出信号连接回路
若驱动器完成上电初始化,右侧光耦导通,左侧形成回路,上位机RDY接口接入24V-电压。反之,上位机该引脚处于悬空状态。以S-RDY为例,
5 共地处理
为了使上位机可以控制驱动器,两者的是需要共地的,否则会使信号传递不稳无法成传递信号。这在CNC的电源线中已经得到保证,即XS1(数控电源口)的4脚(代表信号24VG)已经和24VG连接。此外也可以通过XS10和XS20的1,2,14,15脚接24VG,这样也可以对XS1线的4脚起到分流作用,提高开关量的抗干扰能力。
控制信号共地处理主要是为了提供一个参考电平,在系统中就可以形成一个回路。信号的传递主要需要形成电流回路,为此有必要将供电电源的24VG端连结到一起,如图,为了使CNC伺服的伺服允许Y0.2信号可以控制伺服使能接通与断开,必须使数控系统的NPN输出端所提供的24VG信号连接到直流电源负端。
6 驱动器其他控制模式接线方法
驱动器的其他输入/输出控制信号均是根据实际需要接入,但伺服使能信号必须接入。
且不同型号的伺服系统可能在具体的端口定义和信号形式上有所区别,但是只需要很据其信号名称找到相应引脚和端口,再接入该信号即可。
7 主轴单元电气设计
对于双系统数控铣床其主轴采用变频器+主轴电机控制,且变频器由数控控制。图为主轴单元控制系统原理图。变频器与数控装置的信号连接包括:
(1) 数控装置控制变频器的正反转信号;
(2) 数控装置发送至至变频器的速度或频率信号;
(3) 变频器至数控装置的故障显示等状态信号(考虑到无主轴编码器暂未接入)。
因此数控面板目前只能控制电机转速和正反转,无法显示变频器工作状态。但针对该铣床的实际用途,目前的配置可满足。
变频器的原理和交流伺服电机相近,所不同的是变频器没有主轴电机的反馈信号,也没有伺服驱动器的三环控制电路。只有“交-直-交”的转化过程。
变频器的配线部分,分为主回路和控制回路。对于双系统实验台其配线如下图所示
8 传感器信号转化设计
车床和铣床数控系统HNC-21的开关量输入接口为NPN型开关量输入接口,需要外部提供24VG的信号才能使数控系统的X、Y、Z轴限位开关信号处的光电耦合导通。即需要在限位开关动作后给予X0.0-X0.7引脚24VG信号。
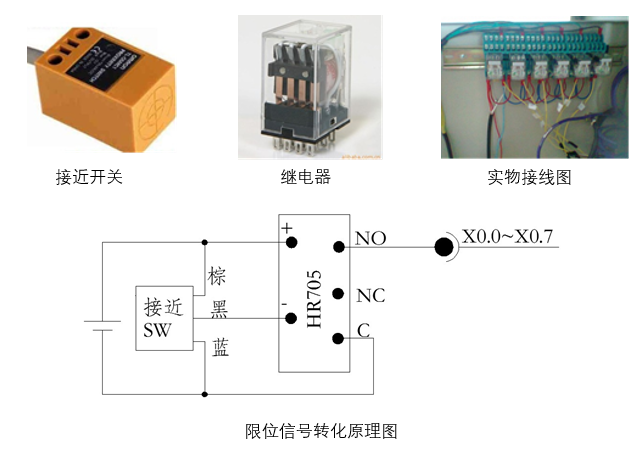
上图为限位信号转接的原理图。将限位开关的黑色信号线与继电器主触点负端连接,主触点正端接入24V信号;且辅助触点的一对常开点NO和C分别接入上位机的响应输入信号接口和24VG。如此,在无信号接入时由于继电器主触点两端均接入24V信号所以辅助触点不动作,数控系统的限位信号输入引脚悬空;接近开关动作时,其黑色信号线输出0V,进而主触点线圈通电,辅助触点动作,常开触点吸合使NO和C导通,从容向数控系统中送入24VG信号。
9 双系统数控铣床电气柜设计
9.1 CNC安装基本要求
(1) 电器柜和操作台必须有足够的电器安装空间,并且满足相关标准对元器件安装距离、安装空间等方面的基本要求。例如:驱动器与机柜和其他部件的安装间距应大于10cm,以留出足够的通风空间。
(2) 安装有CNC、伺服驱动器、变频器等元器件的电器柜和操作台应该采用密闭设计,防止灰尘、切削液等的进入。
(3) 封闭的电器柜需安装散热扇以保证内部空气的循环,例如:驱动器的使用寿命和环境温度密切相关,所以散热扇的安装将会延长驱动器的使用寿命。
(4) 电气柜与操作台的设计、元器件布置、安装位置必须考虑操作、接线、测量、调试、维修与元器件更换的方便。
(5) 对于元器件的布置来说,除了需考虑美观、整齐、方便外,还需要从元器件的散热、防止电磁干扰等方面综合考虑,需要注意:
a) 安装需要牢固;
b) CNC、伺服驱动器、变频器安装方式应有助于散热。
9.2 电气连接的基本要求
正确的连接是系统正常工作的前提,否则会引发故障甚至是重大的事故。在实行电气连接之前一定要对系统各部分的原理要熟练掌握。总的来说连接需要注意以下几点:
(1) 对于电源电压、电源类型、极性必须在仔细检查,确保正确。对于直流电的连接需要注意正负电压的极性,否则会烧毁元器件。对于交流电来说,最好按照规定区分火、零、地线,且电源开关安放在火线上。
(2) 为使电气连接可靠,需要用锡焊。并用绝缘胶布确保被连接处的绝缘。
(3) 为了连接和维修时方便,相同的极性最好使用同一种颜色的线。例如正极采用红色线连接,负极采用黑色线接入。且需要在一些容易弄浑的地方贴标签。
(4) CNC模块、连接电缆的插拔应在CNC断电情况下,并按照规定的方法进行操作。
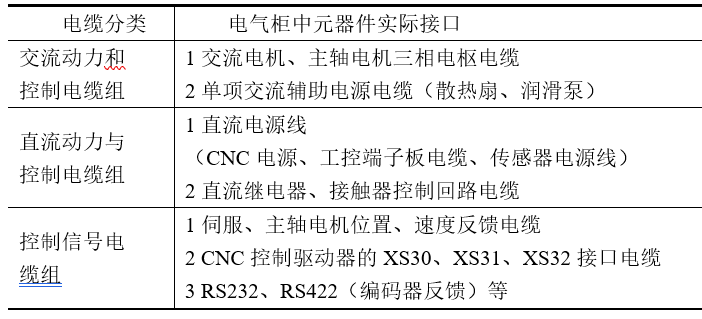
9.3 电气柜元器件连接电缆分组
考虑到上述要求我们设计了数控铣床的电气柜。是实物图如下(电气柜的布线图见附录4).
(1) 控制电源的切换设计
对于双系统数控铣床其控制信号由CNC或工控机提供,在实验前选择其中一个上位机做实验,因此需要进行控制电源切换。我们将24VG端口直接和数控系统(XS1口引脚4)以及端子板的24VG连接,而24V+信号则通过三位开关进行切换。
(2) 控制端口的切换设计
本实验台在实验前不仅要选择上位机的电源,而且要切换驱动装置的控制信号
由于数控铣床是三个进给轴,为了防止日后插拔方便以及防止轴号对应错误、所以将三个坐标轴对应驱动器的转接口做成DB25、DB37、DB50三种类型。且数控的转接口直接安装在安装板上,而工控机的转接口则通过在一块钣金件安装在控制柜的安装板上;且D型口的安装借鉴PC机上的安装方法。实物图如下图所示。
对于变频器,根据目前的需要其控制信号线为4线,即正反转、模拟电压输入。其信号转接用VGA转接口。目前由于本实验台的运动控制卡不支持主轴功能,所以工控机的变频机口暂且保留。其母头由上位机相应的输入信号引脚转接固定到安装板上,而公头由变频器控制信号端子引出的.
对于限位开关信号,转接时需要6个引脚。其母头由输入信号引脚转接固定到安装板上,而公头由机床6个限位开关的控制信号引出。
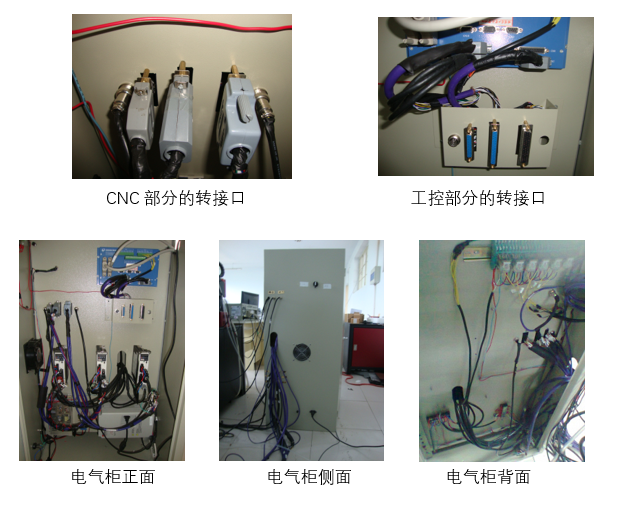